以下內(nèi)容由深圳市金怡智能有限公司(專注電池設(shè)備,電池試驗(yàn)線/中試線/生產(chǎn)線定制)提供:
電動(dòng)汽車上的電池包是一顆顆電芯通過焊接等手段進(jìn)行串并聯(lián),組裝成電池系統(tǒng)放置在箱體內(nèi)。圓柱形鋰離子電池制造工藝,包括勻漿、涂敷、碾壓、分切、烘干、卷繞、裝配、清洗、化成、老化、后處理分選、外觀檢查和出貨。
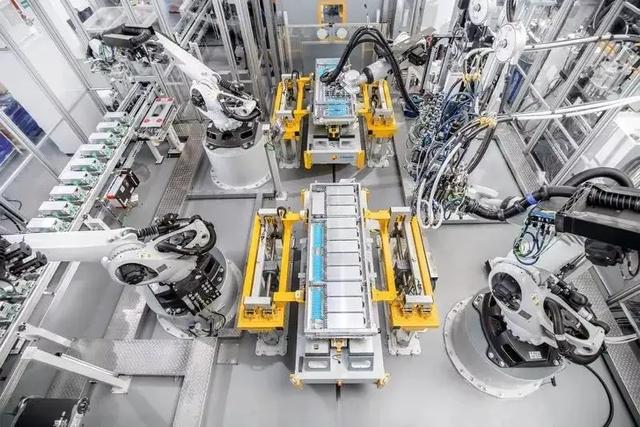
(1)勻漿工藝勻漿工序不再使用傳統(tǒng)的行星制漿機(jī)混漿方式,采用了新型混漿設(shè)備雙螺桿擠出機(jī),創(chuàng)新了混漿方式。這種新型混漿方式能耗低,占用空間小,可實(shí)現(xiàn)正、負(fù)極各3t/h的產(chǎn)量,單條生產(chǎn)線每年生產(chǎn)效率可達(dá)5.4GW·h,大大提高了混漿的產(chǎn)能及效率。
擠出機(jī)混漿設(shè)備具有高精度的喂料系統(tǒng),從下料到出料的混漿過程只需要1min不到就可以完成,從而實(shí)現(xiàn)了連續(xù)混漿生產(chǎn),這種新型混漿方式自動(dòng)化程度非常高。
(2)涂敷工藝涂敷工序采用1.8m寬幅雙層設(shè)備,涂敷速度可達(dá)100m/min以上,每條生產(chǎn)線的產(chǎn)能可達(dá)5.2GW·h。
該項(xiàng)目采用雙面涂敷技術(shù),分為A、B兩頭,B頭接收到的是A頭涂敷完成的單面極片,從烘箱出來(lái)后,經(jīng)過在線動(dòng)態(tài)測(cè)厚儀,實(shí)時(shí)監(jiān)控涂敷的面密度,然后B頭對(duì)極片進(jìn)行返雙涂敷,再進(jìn)入烘箱2層,進(jìn)行烘干。
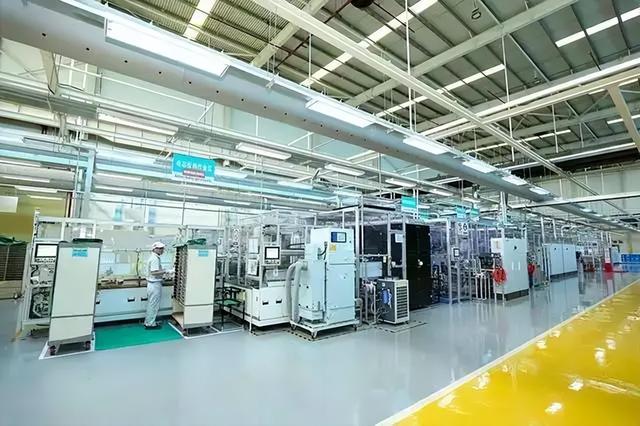
烘箱結(jié)構(gòu)共8節(jié),采用了納米蒸汽+熱風(fēng)烘干的混合加熱技術(shù),可以提高極片烘干效率和極片的黏結(jié)力。而納米蒸汽可以直接穿透涂層,溫度從極片表面至基材表面分布均勻,使得極片的烘干由內(nèi)至外,降低黏結(jié)劑的上浮。
收放卷單元采用自動(dòng)換卷方式,大大提高了生產(chǎn)效率。分切單元將寬幅極片切成兩個(gè)窄幅極片,將分切好的極片進(jìn)行收卷,發(fā)送到下一個(gè)工序。每臺(tái)涂敷設(shè)備采用3臺(tái)測(cè)厚儀在線檢測(cè),可以實(shí)時(shí)監(jiān)測(cè)箔材基底、涂敷單面和涂敷雙面的面密度,實(shí)現(xiàn)定位調(diào)整,極片涂敷質(zhì)量得到優(yōu)化。
(3)壓切工藝極片烘干后進(jìn)入壓切工序,正極采用液壓伺服控制壓輥,采用液壓伺服控制的好處是控制精度高,極片輥壓厚度均勻,主要工藝流程是先上卷再經(jīng)過輥?zhàn)?/span>壓實(shí),接著是測(cè)厚儀在線檢測(cè)極片的厚度,后進(jìn)行收卷。正極碾壓機(jī)還采用了熱壓技術(shù),能更好地控制壓實(shí)密度和壓后極片厚度的均勻性。
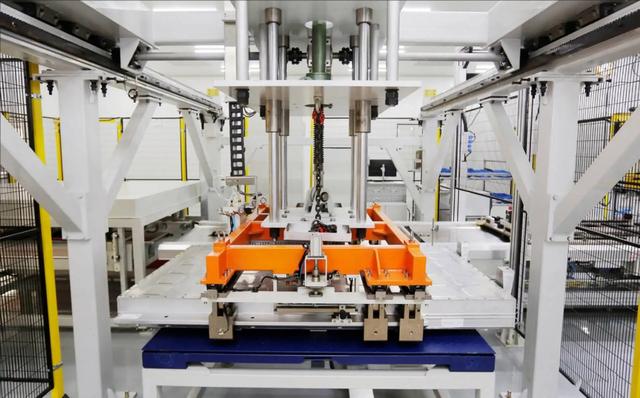
負(fù)極采用二次碾壓工藝,就是極片經(jīng)過兩組壓輥。采用二次碾壓工藝可以很好地保證極片的厚度控制在正常范圍之內(nèi),碾壓過后還要經(jīng)過一個(gè)S形的烘箱再次烘干,可以防止水分影響極片的厚度,后收卷。
分切機(jī)將壓好的極片分成符合加工電池寬度的極片,分切機(jī)刀具采用上下都有弧度的刀片,這樣切出的極片外觀更好,毛刺更少。該項(xiàng)目還采用了CCD在線檢測(cè)系統(tǒng),發(fā)現(xiàn)外觀不良后會(huì)自動(dòng)貼標(biāo)簽,在后續(xù)卷繞過程中自動(dòng)去除,可很好防止產(chǎn)生不良電芯。
(4)卷繞工藝卷繞車間整體環(huán)境溫度控制在18~26℃,濕度控制在1%以下,粉塵度控制在10000級(jí)以下。前面工序制備好的正負(fù)極片通過AGV自行運(yùn)送到烘干車間,運(yùn)輸過程中采用全密封箱體轉(zhuǎn)運(yùn),可以有效控制運(yùn)輸過程中極片的水分含量。在卷繞前,極片需要經(jīng)過高真空烘干,大限度地去除極片中的水分,保證產(chǎn)品質(zhì)量。烘干過程采用自動(dòng)呼吸式的流程控制,以氮?dú)?/span>作為保護(hù)氣體,以達(dá)到升溫和降溫的作用。
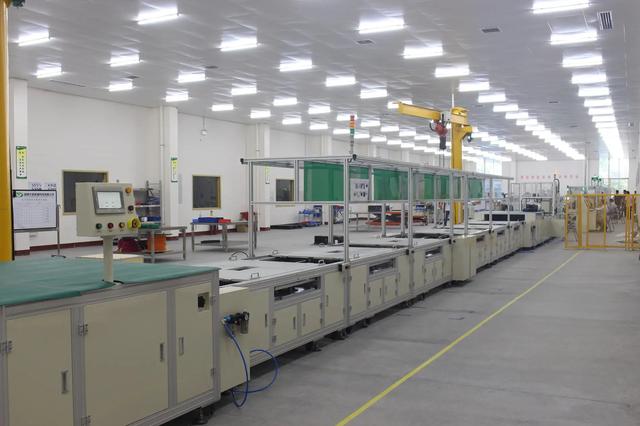
卷繞機(jī)具備連續(xù)自動(dòng)換料、下料功能,還具有極耳雙面焊接切換、負(fù)極銅箔外包或隔膜外包切換、電極漿料切斷和極組整形等功能,增加了膠帶、極耳等多項(xiàng)在線檢測(cè)功能,所有在線檢測(cè)不良品會(huì)被自動(dòng)排除,設(shè)備可靠性很高。
該工序主要原材料的投入、制造過程信息和人員信息均上傳至MES進(jìn)行監(jiān)控,對(duì)原材料的先進(jìn)先出、干燥時(shí)間控制、原材料規(guī)格和批次信息追溯等均可在線監(jiān)控,真正做到生產(chǎn)過程的信息化和自動(dòng)化。
(5)裝配工藝卷繞好的極組被送到裝配車間,采用先進(jìn)的圓柱形電池組裝生產(chǎn)線,速度相比一般至少速度提升54%。裝配過程中需要用到的設(shè)備如下:
1)上料機(jī):其主要功能是完成上料并將極組裝入電池殼中。上料機(jī)采用小車自動(dòng)上料,工作人員只要將小車推到指定位置,設(shè)備就能完成自動(dòng)上料。在上料時(shí)能夠自動(dòng)記錄產(chǎn)品批次,進(jìn)行追溯。
2)負(fù)極耳焊接機(jī):其主要功能是將負(fù)極耳與電池殼進(jìn)行焊接,可實(shí)現(xiàn)單層、雙層的銅極耳、鎳極耳等不同極耳的焊接。
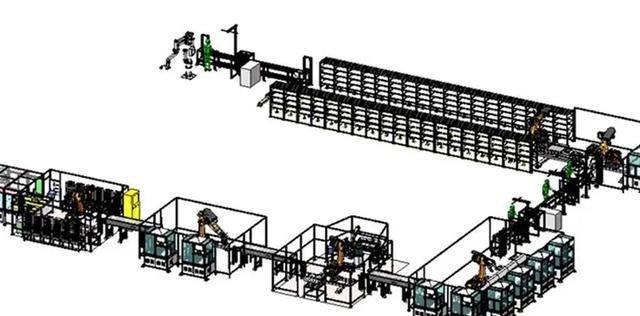
3)收口與滾槽機(jī):為了盡可能利用電池殼的內(nèi)部空間,采用了T形殼的設(shè)計(jì),就是口部外徑要大于殼身外徑,因此設(shè)置了收口工位,經(jīng)過該工位后,電池殼的口部外徑與殼體外徑一致。滾槽機(jī)的每個(gè)工位都設(shè)置了吸塵功能并由傳感器對(duì)吸塵器內(nèi)的真空度進(jìn)行檢測(cè),有效降低了因金屬粉末掉入電池內(nèi)部而造成電池性能下降的風(fēng)險(xiǎn)。
4)注液機(jī):它是裝配線的核心設(shè)備,其采用了托盤式注液及腔體式加壓的方式。在注液機(jī)內(nèi)部設(shè)置了排風(fēng)與漏點(diǎn)檢測(cè)儀,有效提高了注液的準(zhǔn)確性與電解液的浸潤(rùn)效果,降低了電解液在車間內(nèi)的擴(kuò)散。
5)封口機(jī):封口機(jī)操作分為3個(gè)步驟,分別是預(yù)封、卷邊與下壓。經(jīng)過這一步操作電池完全成型。
裝配線上大量采用了CCD與傳感器檢測(cè),根據(jù)實(shí)際產(chǎn)品特性采用了新的檢測(cè)參數(shù)與方式,不僅提高了檢測(cè)準(zhǔn)確度并增加檢測(cè)內(nèi)容,還可以實(shí)現(xiàn)產(chǎn)品所有關(guān)鍵參數(shù)的在線檢測(cè)。該裝配線還實(shí)現(xiàn)了在線自動(dòng)預(yù)化成功能,這樣既節(jié)省了操作人員的工作量,又有效控制了清洗至預(yù)化成的時(shí)間,進(jìn)而降低了生銹的風(fēng)險(xiǎn)。
(6)化成工藝化成車間的功能是完成電池的活化及分容。車間內(nèi)配置了一整套全自動(dòng)化成設(shè)備及智能物流運(yùn)輸系統(tǒng),包括調(diào)度系統(tǒng)、充放電設(shè)備、倉(cāng)儲(chǔ)設(shè)備及輸送設(shè)備。電池自投入至產(chǎn)出,全程無(wú)需人員參與。
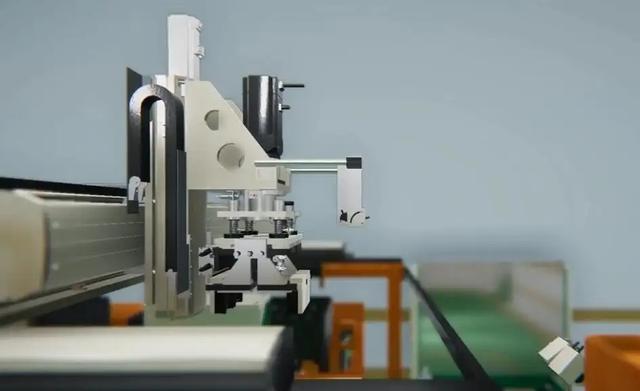
1)調(diào)度系統(tǒng)布局在車間二樓,是整個(gè)車間的神經(jīng)中樞,具有控制、監(jiān)控、數(shù)據(jù)收集及存儲(chǔ)、邏輯運(yùn)算等功能。
2)充放電設(shè)備共有5條線體,可同時(shí)對(duì)上百萬(wàn)只電池進(jìn)行充電和放電,充放電設(shè)備采用能量回收系統(tǒng),可將電池放電時(shí)的電能回收至電網(wǎng)。在異常狀態(tài)下(電池爆噴),會(huì)有溫度、煙霧報(bào)警,設(shè)備自身可實(shí)時(shí)檢測(cè)電芯狀態(tài),有效避免危險(xiǎn)事故的發(fā)生。
3)倉(cāng)儲(chǔ)設(shè)備分為高溫老化間和常溫靜置區(qū),區(qū)域每個(gè)倉(cāng)位配有煙霧報(bào)警器。當(dāng)有危險(xiǎn)事故發(fā)生時(shí),堆垛機(jī)可迅速將危險(xiǎn)托盤運(yùn)送至鹽水箱進(jìn)行控制。
4)堆垛機(jī)在系統(tǒng)指令下,自動(dòng)搬運(yùn)電池,完成上料和下料動(dòng)作。
5)分檔機(jī)有6臺(tái),每臺(tái)分檔機(jī)有8個(gè)工位,可自動(dòng)將電池依據(jù)電壓內(nèi)阻容量進(jìn)行分檔操作,分檔后的電池再經(jīng)過外觀檢驗(yàn)包裝出庫(kù)。
部分內(nèi)容素材來(lái)源于網(wǎng)絡(luò),如有侵請(qǐng)聯(lián)系金怡智能小編,將在第一時(shí)間為您處理
好了,這篇文章的內(nèi)容發(fā)貨聯(lián)盟就和大家分享到這里,如果大家網(wǎng)絡(luò)推廣引流創(chuàng)業(yè)感興趣,可以添加微信:80709525 備注:發(fā)貨聯(lián)盟引流學(xué)習(xí); 我拉你進(jìn)直播課程學(xué)習(xí)群,每周135晚上都是有實(shí)戰(zhàn)干貨的推廣引流技術(shù)課程免費(fèi)分享!